top of page


ACCELERATED SURFACE FINISHING
Accelerated Surface Finishing is our proprietary Isotropic Superfinishing process, designed, engineered, and produced in house. ASF is capable of producing surface finishes otherwise unachievable through "standard" vibratory finishing processes. The ASF process is a proven technology in many manufacturing disciplines, to reduce wear, improve duty life, reduce corrosion inheritance, and reduce noise along with other tribological benefits.
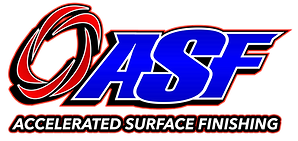
PROVEN INDUSTRIES & APPLICATIONS
PULP & PAPER
TRUCKING
HEAVY EQUIPMENT
DEFENSE
AEROSPACE
HIGH PERFORMANCE AUTOMOTIVE
POWER GENERATION
MEDICAL DEVICE
ADDITIVE MANUFACTURING
BEARINGS
GEAR MANUFACTURING
MINING
AGRICULTURE
PETROCHEMICAL
MARINE TRANSPORT
PHARMACEUTICAL
RAILROAD
FOUNDRY
MACHINE TOOLS
SALVAGE
AIR TRANSPORTATION
PLATING
CUTLERY
HOW IT WORKS
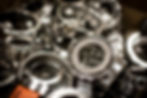
An Accelerated Surface Finishing process is completed in a "mass finishing" environment, otherwise known as vibratory finishing. These machines can consist of the well known "standard" machines but also in high energy or centrifugal finishing equipment.
Process development starts from determining what material is being processed and a proprietary chemical formulation is selected to react with the substrate material at specific concentrations and flowrates.
The chemistry forms a film that is continually formed and wiped through the motion of the selected piece of equipment slowly refining the asperities of "peaks" of the surface profile. The media in the machine is a specific bond containing no added abrasive characteristics thus imparting the innate texture of the media onto the substrate itself. Due to the lack of abrasive profile in the media, the component substrate is left with low Ra surface values once the process is complete.
WHY IT WORKS
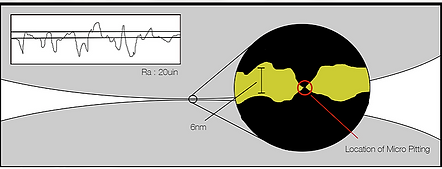
BEFORE ASF

Manufacturing a component - specifically a toleranced critical surface - gets honed, ground, or otherwise machined, leaving directional topography on a part surface. Based on the technique used, this topography can be visible to the eye or under magnification.
No matter how microscopic this texture may be, it will affect the part to part interaction, windage, wear and tribological properties of the components.
You can only expect your lubricant to do so much. The tolerancing of components is predicated on a lubrication wedge that is responsible for keeping the components from contacting each other and creating friction - causing heat - causing viscosity alterations - causing micro-pitting - causing spalling - causing failure.
AFTER ASF
The distance between components, defined by the lubrication wedge can be microns wide - necessitating surface roughnesses to be equally sized. If a ground surface has asperities (peaks) over the given wedge value, the parts will ultimately contact each other, propagating a micro-pit. An ASF processed component can resist this type of wear significantly better than a precision honed component.
TALK WITH US!
ISOTROPIC FINISHING IS NOTHING NEW!
"The term "isotropic" has been around as long as vibratory finishing itself, plainly meaning "non-directional".
ASF and other similar technologies have raised the bar on what traditional vibratory finishing was capable of and given new meaning to "isotropic".
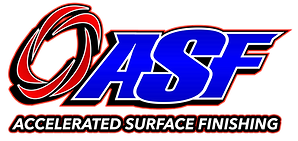
"Your process is better than what we have been using. We are excited to move our process to ASF"
Let's talk about your current Isotopic Superfinishing system or prospective projects. Our Sales Engineers will help you through and challenges and offer competitive and useful insight so you can make the right decisions for your process.

LOOKING FOR MORE RESOURCES?


bottom of page